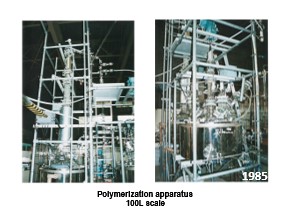
The Teruo Fujimoto Laboratory at Nagaoka University of Technology has been working on increasing the size of anionic polymerization equipment since the early 1980s. The laboratory has successively installed and operated four large anionic polymerizers. The first was used for charge mosaic membrane, the second for oxygen-enriched films and monodisperse KrF resist, the third for functional paints with pigment binding sites, and the fourth for polymers for all-solid-state batteries.
The second unit (Figure27) was constructed in 1985. The polymerization vessel was 100 L, and the distillation column was 5 m high, made of all QVF glass. The polymerization scale was normally 5Kg, and anionic polymerization up to 10 Kg could be performed. Incidentally, the second and fourth units were designed by me.
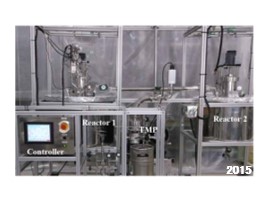
Figure 28 shows the large-scale anionic polymerization apparatus. This apparatus consists of stainless steel reactor with high-speed rotating fin, electrical controller and turbo molecular vacuum pump. Attained evacuation of total system is < 5×10-5 Pa. Helium leak rate of total system is < 5×10-9 Pa・m3/sec.
After setting of monomers, solvent, initiator and quencher to this apparatus, temperature and pressure can be controlled and multiblock copolymers with narrow molecular weight distribution are synthesized automatically. By using the apparatus, 3 kg of the block copolymer is synthesized in single batch. Incidentally, the equipment was designed and manufactured by us and is completely original.
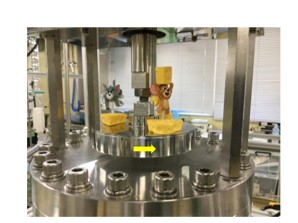
The stirring blades inside the twin reactor are rotated by powerful magnets. The rotation speed can be set arbitrarily from 1~1000 rpm. A Tom and Jerry doll (Figure 29) is attached to the top of the magnets, which soothes the hearts of tired researchers on a daily basis. (Sometimes, it is replaced by the Jurassic Park version.)
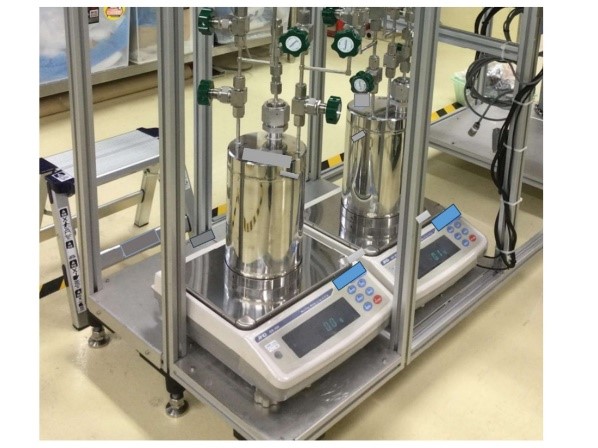
The amount of monomer used for anionic polymerization is controlled using a precise electronic balance. The total weight of the monomer and the container containing the monomer can reach 10 kg, but the error in the amount of monomer to be fed is < 0.1 g. (Figure 30)
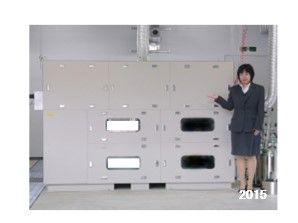
Figure 31 shows our newly designed and fabricated continuous anionic polymerization system. Although only homopolymers can be polymerized so far because they were originally developed for other applications; by continuously feeding monomers, hundreds of kilograms of polymer can be synthesized in a single day. If it is to be used for the production of base polymers for KrF resists, the quantity and quality will be satisfactory enough.
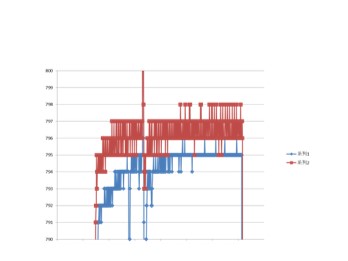
Figure 32 shows the feed output of the continuous polymerize. The feed errors for both feed series 1 and 2 are ±0.15%, which enables highly accurate polymerization. The system is equipped with a temperature sensor, pressure sensor, precision feed pump, precision balance, and Coriolis flowmeter. The inside of the apparatus is sealed with nitrogen gas, which has been approved by the fire department as an explosion-proof structure. A WD filter is installed on the left hand side of the apparatus to enable immediate re-precipitation of the polymer solution.
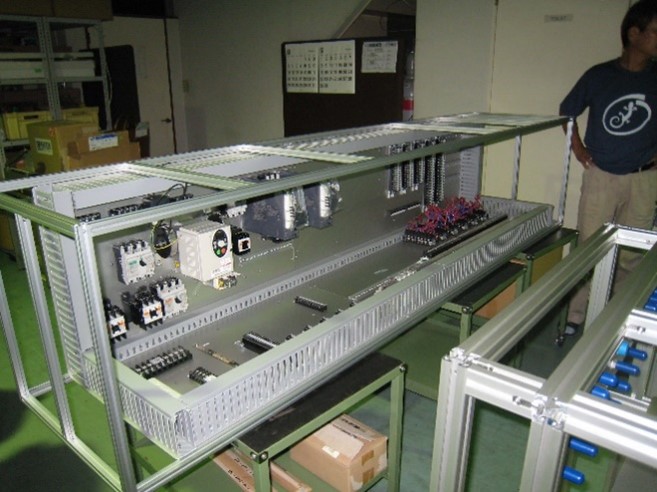
Figure 33 shows the fabrication of the continuous polymerization system. The equipment is completely original, and everything from design to assembly is done by our own hands. Although the number of team members is small, each of them is a highly specialized and capable person.
Our ultimate targets are ① the fabrication and operation of a large anionic polymerization system of 1000 L or more, and ② the development of a tabletop anionic polymerization system. It goes without saying that ① is a batch-type HVM system, but ② will be the ultimate continuous anion polymerization system. This equipment will continue to synthesize polymers continuously, and will continue to produce block copolymers at the same level as the batch type. Incidentally, the drawing of the apparatus has already been completed.